In today’s entry we are going to look at weighing scales that are designed to weigh 55 gallon drums with ease. There are quite a few scale choices out there from the Brecknell DS1000 to the Rice Lake Roughdeck BDP and everything in between.
There are numerous things took look out for when you are looking to purchase a drum scale. We’ve seen some pretty good choices that are relatively affordable and we’ve seen some affordable scales that are not very good or repeatable.
Thoughts on the Rice Lake BDP Drum Weigher
When you’re in the market for a drum scale, first decide what brands and/or price range you are interested in. We mention this because the quality, accuracy, and consistency of Rice Lake Roughdeck BDP drum scales is going to be higher than some of the low cost platform scales you might find online. Why you might ask? One reason is the load cells. Of course, these systems are also likely going to cost more money as well.
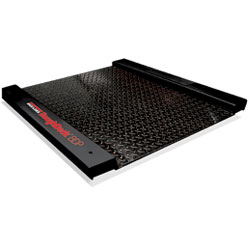
Painted Steel Drum Scales for Steel Weighing?
While we’re at it, just to be clear, don’t confuse these low profile drum scales with a steel drum scale. The latter are sometimes mentioned as choices for weighing large steel coils, which is not what a drum scale can accommodate.
Ok, now that we have that out of the way….
A lot of industrial warehouse locations or perhaps a busy shipping area where goods are constantly being moved around by a pallet jack can use a drum weigher. A drum scale is typically a low profile floor scale that is actually a lower profile than a traditional 4×4 floor scales that virtually every warehouse utilizes.
Drum scales can be used with or without one or more ramps. Other weight choices to consider with a drum scale system include digital weight indicator features such as LCD display, RS-232 communication for connecting to a printer or computer, or battery power. Battery power is helpful and would allow the scale to be installed in remote locations where a power outlet might not be available. Another feature that is handy for a portable application would be either a portability frame, wheels, or two handles.
What are the Capacities and Readabilities of each model?
An imported drum scale platform typically features integral ramps, live side rails, wheels, and handles for the ultimate in versatile weighing. The majority of drum weighing scales are available in 500, 1000, or 2000 pound capacities. Popular platform sizes of most drum scales are typically somewhere around 30″ x 30″ or 36″ x 36″.
Also, it’s worth mentioning a special note regarding dimensions. You will want to make sure what dimensions you are going by when choosing a drum scale. Obviously, you want a low profile scale that is easy to roll heavy drums onto. But, there are the overall dimensions and there are the actual low profile platform portion of the scale to consider as well.
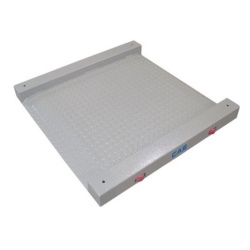
Thoughts on the CAS Corporation R2 SERIES DRUM SCALE
The CAS R2 Series Drum Scale stands out for its numerous features that make it a versatile and portable weighing solution. First, it is constructed with reinforced mild steel, ensuring durability and longevity. The anti-skid diamond plate deck guarantees a secure grip for the drums being weighed. The light weight R2 Series has two heavy duty handles and two casters built into the frame. Need to move your scale? No problem. Pick it up and roll it. It’s that easy! This product is manufactured overseas but supported by CAS USA headquartered in NJ.
One of the key characteristics of this drum scale is its portability. The integral ramps make it easy to roll drums onto the scale, and the live side rails provide added safety and stability during the weighing process. The scale is also equipped with built-in casters, allowing for effortless transportation from one location to another. Additionally, handles have been included to further enhance portability.
Lastly, the CAS R2 Series Drum Scale comes with a 1-year warranty, providing peace of mind to users. This limited warranty covers defects in workmanship during the first year of use.
What are the features of the Brecknell DS1000 Drum Scale?
The Brecknell DS1000-LCD Drum Scale boasts a range of impressive features that make it an excellent choice for bustling shipping areas and drum weight monitoring. Designed to handle the constant movement of goods by pallet jacks, this scale is both portable and low-profile. Its rugged steel deck is powder coated for durability, ensuring that it can withstand heavy use.
One standout feature of this scale is its unique 9% entry and exit ramp, which facilitates easy rolling of drums on and off the platform. This gradual incline eliminates any hassle or difficulty when maneuvering drums, saving time and effort.
With its user-friendly design, the imported Brecknell DS1000-LCD Drum Scale is incredibly simple to operate. Its indicator offers a comprehensive range of weighing functions, making it suitable for a wide variety of applications. Additionally, it features a display-hold function, allowing users to retain results on the screen for reference.
This scale is highly versatile in terms of power options. It can be both AC and battery powered, enabling installation in remote locations where power sockets may not be readily available. This portability allows for greater flexibility in using the scale wherever it is needed.
Key Points to Know about Electronic Scales for Weighing a 55 Gallon Barrel
Most drum scales, which can also be called barrel weighing scales, are constructed of painted steel. The actual weighing platform is usually a diamond tread design. You can also get a stainless steel drum scale as well. Items can be weighed on the scale platform and/or across the side rails for larger items. A low profile design with ramps can be a great choice for dollies, wheeled carts with a drum to be easily rolled onto the platform.
In most cases, drum scales are designed to be durable and accurate. But, they are also designed to be lightweight and portable in many situations. That is a balancing act for many situations. In order to make a drum scale portable, it needs to be able to roll and be light enough for an average person to pick up on it’s side.
One of the issues that we sometimes see with drum scales is a tendency for the scale to be dropped. This can happen fairly easily. Someone sets the drum scale on its side and rolls it to a new location. They set the scale up against the wall and leave it. Then someone else comes by and knocks the scale platform over.
This can be a problem if precautions are not taken into consideration. Knocking over a scale can damage a load cell, bend or break a foot, and lead to down time without a scale.
Drum Scale Final Thoughts
We hope this article on 55 Gallon Drum Scales Buying Advice has helped you better understand the overall drum scale market. In our opinion, if you can afford it, a drum scale from a scale manufacturer like Rice Lake is a better choice for industrial applications than some of the low cost options in the marketplace which use really cheap components, especially when it comes to load cells and summing boards. The Rice Lake version is generally more consistent, accurate, and serviceable with shear beam load cells that can actually be replaced if necessary.
To Order or Request a Quote
Please contact our sales department if you need any assistance or quotes on any of our products.