DETECTO’s USA-made HealthySole® is the first clinically-proven UVC product to kill up to 99.99% of exposed microorganisms, such as bacterial and viral pathogens, on the soles of shoes in 8 seconds. HealthySole® is also effective against fungi and bacterial spores that travel on shoe soles leading to the spread of infection via inhalation or horizontal translation from surface and air contamination. By adding HealthySole® to an existing infection control program, the facility will decrease the overall microbial load starting with shoe and floor contamination.
HealthySole® HSPlus UVC Disinfection System significantly decreases the aerosolizing, migration, or transfer of deadly pathogens that lead to higher healthcare-associated infections (HAI) rates. HealthySole® is green technology that disinfects without using harmful chemicals. ETL/CETL and CE listed.
Below is a list of frequently asked questions that customers are curious about before making a purchase.
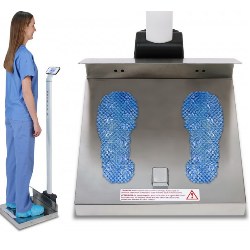
Q. So how does your product work?
A. Upon entering the O.R. corridor either through the front entrance or through locker rooms, each clinician would step onto the Healthysole® Plus device. The HealthySole® Plus informs the clinician that their shoes are properly aligned and starts an 8-second count down opening up the shutters and exposing the soles or booties to the germ killing ultraviolet light. At the end of eight seconds a green check mark appears letting you know the process has been completed.
Q. Are there any studies that show the quantitative reduction of HAIs in a certain hospital once HealthySole® Plus was introduced?
A. In today’s battle of fighting HAIs, hospitals are using an arsenal of UVC products and equipment such as robots or air and water treatment systems to kill pathogens from those reservoirs. This lack of options is leaving the shoe soles untouched. To answer your question, three independent third-party laboratories including the Cleveland VA, Texas Medical Center Houston and Microchem Labs have tested and proven an over 99% kill rate for MRSA, VRE, CRE, Streptococcus and Pseudomonas.
Q. What will HealthySole® Plus do differently compared to other disinfectants or types of new technology such as whole room plasma machines, UVC robots or chemical environmental decontamination?
A. HealthySole® Plus is an active 24/7 chemical free, UV disinfection technology that when stood on will consistently lower the over microbial load throughout a healthcare environment and even more specifically in the targeted environment. The best
practice for infection control programs is to bundle all the necessary effective technologies to address every potential vector for the spread of infectious pathogens. There is no silver bullet; however, when technologies and chemicals are bundled properly the highest potential for environmental de-contamination is achieved.
Although technology such as ion disinfection systems are an attempt at 24/7 disinfection technology, they only theoretically lower the load in the particular room they are used in and don’t treat the shoe soles nor stop the spread of organisms from entering or exiting an environment. There are areas within healthcare that cannot use this type of ionization or other aerosol or mist technologies. HealthySole® Plus can be used in any environment in healthcare even in conjunction with technology such as these.
UVC robots are a good use of UVC technology to reduce microbial load on visible surfaces. Any shadowed or obscured area is not treated. As well, they do not address the spread of organisms entering and exiting environments via shoe soles. The first person to walk into a robot-decontaminated room will re-introduce all the infectious organisms via shoe soles to that room. Also, UVC robots treat rooms on a case-by-case basis, which requires added healthcare personnel to manage the unit each time it is placed in a room. People cannot be present while this technology is in use, which is contrary to the use of
the HealthySole® Plus. HealthySole® Plus can be placed at any room or hallway where people are present 24/7 and work in tandem in rooms where robots are deployed.
Chemicals are also good for environmental cleaning purposes; however, they are not used all day long, nor can they keep the floors clean when shoes step on a previously de-contaminated floor. Although chemicals are very necessary, they are a quick fix of a contaminated or soiled location, which will be rapidly re-contaminated. Chemicals often cannot be deployed often enough, fast enough, or in certain environments. Because HealthySole® Plus is a non-chemical use of disinfection technology, it can be used constantly by staff and placed anywhere in a healthcare environment and again work side-by-side existing chemical protocols.
Q. Do we already have established protocols for Hospital Departments?
A. Protocols for HealthySole® Plus in different departments will vary depending on each hospital. The layout, size and traffic flow of the particular department or room will vary from hospital to hospital. For example, if implementing HealthySole® Plus into an ICU, HealthySole® Plus should be placed at each entry/exit point within each separate room. For the highest effectiveness in reducing the overall microbial burden and to reduce the spread of pathogens into and out of the ICU, it should be protocol for all staff and visitors entering and exiting the ICU to stand on HealthySole® Plus (assuming there is not an emergency where a staff member needs to relocate immediately).
If traffic flow is high or if the ICU is divided into separate rooms, HealthySole® Plus units should be added to fulfill the need of separate locations or high traffic volume. This same protocol should be followed in other departments, units or wards such as Dialysis, Wound Care, Cancer Treatment, Burn Treatment, etc.
Operating Rooms and OR corridors also need to have HealthySole® Plus units at each entrance/exit of the critical areas beyond the barrier or “red line.” Hospitals that desire to be most effective in lowering the overall microbial burden inside of each OR, can place a HealthySole® Plus unit outside of each room, designated for the entry and exit of each person to that specific room.
Q. We already have a procedure in place that addresses shoe soles. It is mandatory that all of our OR staff replace booty covers when re-entering the OR area, so why would we need HealthySole® Plus?
A. Studies regarding shoe covers and dedicated theatre booties are both supportive and un-supportive of the practice. If over shoes do decrease the amount of pathogens brought into your OR compared to street shoes, that is good; however, there will still be pathogens present on those booties upon entry. If HealthySole® Plus is used immediately before entering the barrier to the corridor or active OR, the bacterial count will be significantly lower then if not used. By killing up to 99.9+% of the remaining pathogens on the booties or dedicated theatre shoes, you are lowering the pathogenic load in the OR and
decreasing the risk of infections.
Remember, 33-37% of HAIs are surgical site infections, many of which come from the OR. Lastly, booties don’t kill the organisms on the soles of the shoes when applied, they simply cover them up. HealthySole® Plus kills the organisms not allowing them to survive or replicate and lowers the OR environmental microbial burden. As well, the HealthySole® Plus can be used in conjunction with over shoe booties, continuing to further strengthen the hospitals fight against infectious pathogens.
Q. We have constant traffic with staff in and out of rooms; therefore, it’s not realistic to have them stand on the unit for 8 seconds each time.
A. Whether or not we like it, ICUs and PICUs suffer issues from dangerous pathogens and all possible Infectious Control hygiene measures must be used to address this. Shoe soles have been proven to be an unaddressed reservoir of infectious pathogens in a hospital environment and are the first step that leads to infection transmission if not addressed properly. It is recommended whenever possible* to use HealthySole® Plus by each person entering the ICU/PICU for an 8-second kill cycle, in order to reduce millions of organisms from entering that critical environment. *As long as that person is not time restricted due to emergency.
Strict hand hygiene guidelines can be somewhat time consuming however critically necessary. Hand hygiene protocols include the use of gloves, minimal numbers of cleaning locations and dispensers and often suggest washing procedures that can
take up to 2 minutes to be effective. These protocols are required prior to treating a patient; furthermore, they are used between separate tasks on one patient and always between tasks on other patients.
The HealthySole® Plus and its ability to reduce germs within a space means it should be handled like hand hygiene as a major barrier to stop the spread of infectious pathogens in an ICU/PICU as well as other acute areas. This consistent use of the HealthySole® Plus will ultimately keep patients and staff safe and healthy as well as reduce widespread infection within a facility.
Contact our sales team (919) 776-7737 or visit our website to get a quote.